Whether you’ve just opened your first warehouse or you have warehouses in operation across the country, there is always room for improvement and cost-cutting to improve your bottom line. However, you can’t just cut warehouse costs haphazardly. The key to successfully increasing profits in a warehouse is to reduce operational costs while maintaining or increasing the standard of product and service you provide. That’s why we have put together a list of the top ways to save money in a warehouse without affecting your quality of service.
How To Reduce Warehouse Costs
Labour
Labour costs are the leading operating expense in most warehouses. In fact, labour costs can often account for up to 50% of total operating costs in the warehouse. This means that one of the best ways to find room to reduce your warehouse costs is to minimise labour costs.
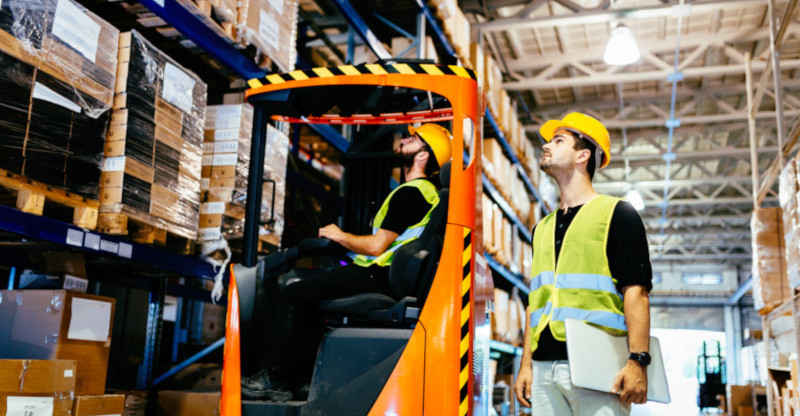
There are two main ways to optimise your spending when it comes to labour costs:
- Improve the training and morale of your workforce
- Review scheduling and employee hours
Training and Morale
Investing in the training of your workers will reduce time and product losses due to mistakes, as skilled workers are less likely to make costly errors. Regular training refreshers will also help to increase the efficiency of your workforce. This in turn will reduce the number of labour hours required to complete the same amount of work.
Although ensuring your workers are happy may not be the first thing that comes to mind when looking to save money in a warehouse, worker morale actually has a significant impact on productivity. In fact, happy employees are up to 20% more productive than unhappy ones. Additionally, improving the morale of your team will increase employee retention, saving you money on hiring and training up new staff.
So, when it comes to saving money in a warehouse, team morale should definitely be a consideration. There are many simple things that can be done to improve worker morale such as investing in an incentive scheme to reward hard working employees, or even just introducing a suggestions box.
Another way to cut costs is through cross-training your workers. This will allow you to avoid hiring new staff when it is not absolutely necessary, and maintain efficiency. To effectively implement cross-training, identify your most reliable and productive workers and cross train them in other areas. This will allow cross-trained workers to help out in other areas when there is a volume increase or in the case of a labour shortage to prevent lost time.
Review Scheduling
Another obvious way to reduce labour costs is by reviewing worker schedules and reducing the number of labour hours scheduled where possible. Cross training workers can be useful in reducing labour hours as you will have the backup of moving a worker from one area to another, rather than having to pay for an additional person to be rostered on just in case the team is running behind or there is extra work to do.
Operations
Alongside labour costs, one of the biggest expenses in a warehouse is space. You will be paying money for every square metre of space in your warehouse, so to increase your return on investment it is important that the space is optimised to maximise storage, streamline operations, and even reduce facility costs. The top two ways to optimise warehouse operations to save money are:
- Optimising storage to increase capacity
- Optimising layout to improve warehouse processes
Optimise Storage
A few factors to consider when optimising your warehouse for maximum storage include:
- Is your space too big for your inventory?
- Are there enough shelves to make the best use of the available space?
- Do you have the right kind of shelving to maximise the storage of your products?
1) Is your space too big for your inventory?
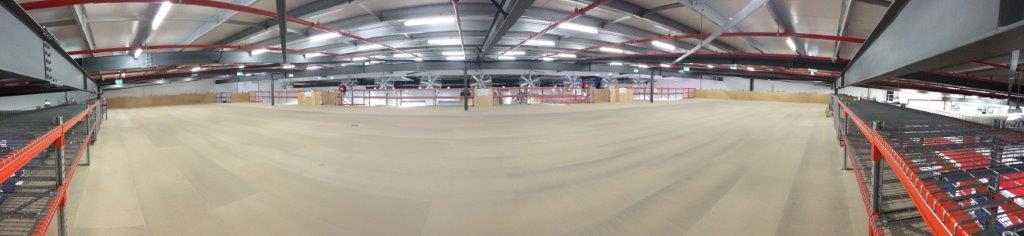
Commercial leases tend to span 5 to 10 years, or even longer. As such, it is common for business owners to plan for future growth by renting out a warehouse that is larger than necessary. However, if your warehouse is too big for your inventory you will be paying for unneeded floor space, and unnecessarily increasing your overhead expenses.
To avoid paying for unneeded space, consider subletting out part of the warehouse to subsidise rental costs. (Be sure to check that the lease agreement allows for commercial subletting first).
Alternatively, if you are expecting considerable growth in the near future, negotiate a commercial lease with a shorter term to give your business the flexibility of moving to a larger premises when required.
2) Are there enough shelves to make the best use of the available space?
Simply adding some additional shelving can dramatically increase the storage capacity of a warehouse, and can also cut down on labour times. For example, pallet racking can be used to optimise storage in an area where pallets are stacked on the floor against a wall by adding a selective pallet racking system. This will increase the number of pallets that can be stored at one time by making use of vertical space, and reduce labour times by making each pallet individually accessible.
3) Do you have the right kind of shelving to maximise the storage of your products?
One factor in optimising storage that is often ignored is whether or not you have the right kind of shelving to maximise storage for your specific products. Each racking and shelving system is designed for different sizes and types of product ranges which is why it’s important to install a pallet racking system that has been designed for your products.
For example, FIFO (first in first out) pallet racking systems are ideal for use where regular product rotation and limited product shelf life are a concern. Conversely, LIFO (last in, first out) storage systems can provide a high density storage solution for product ranges with a low number of SKUs, but may not be ideal for a warehouse with a high differentiation in products.
If you’re not sure which pallet racking system is best suited for your product range to minimise cost and optimise warehouse operations talk to the racking experts at MACRACK. Call us today on 1800 048 821 for a free quote and warehouse layout plan.
Optimise Layout
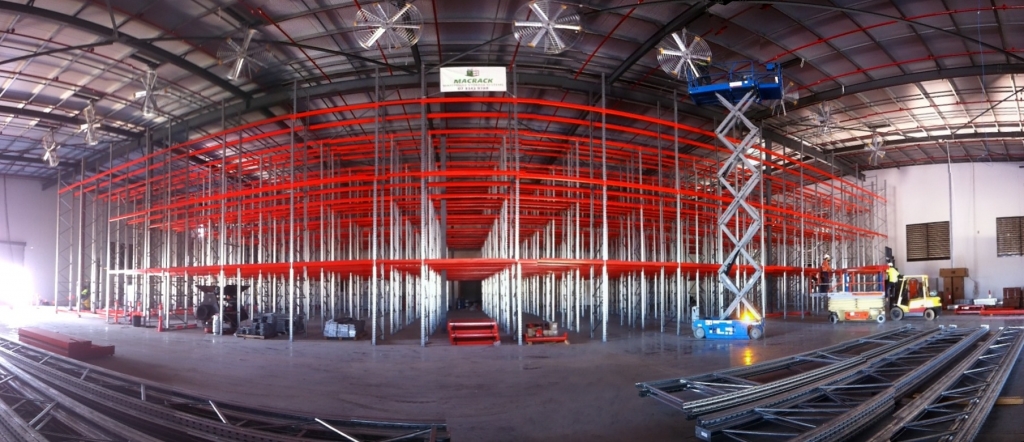
Optimising the layout of your warehouse can improve warehouse operations and subsequently reduce labour hours and costs. It can be useful to hire a warehouse storage professional to evaluate the efficiency of your warehouse layout, and advise on any adjustments that could be made to improve operations and reduce costs.
Alternatively, when conducting your own assessment of your warehouse layout consider the following questions:
- Are the products with the highest turn over stored at the front or bottom of the shelving system for easy retrieval?
- Is every shelf being used to its maximum potential?
- Is the type of shelving you have installed ideal for your warehouse operations?
- Is the space between aisles wide enough for the easy operation of manual handling equipment?
- Are you making the best use of all the space available to you (including vertical space)?
How Can We Help You Save Money In Your Warehouse?
MACRACK has been manufacturing and installing quality pallet racking and shelving systems in Australia for over 40 years. Whether you’re looking to increase storage or optimise your warehouse layout, we’ve got you covered. We can design, customise and install the perfect racking system for your products, add to an existing MACRACK racking system, or even relocate your racking system to a new premises. Call us today on 1800 048 821 for a free quote and plan layout.
